Advanced Techniques in Metal Stamping for Precision Manufacturing
In the world of precision manufacturing, the advancement of metal marking strategies has been a pivotal pressure in accomplishing unparalleled degrees of accuracy and performance. As markets constantly require finer resistances and elaborate layouts in their metal parts, the mission for innovative methods in steel stamping has actually increased. From the usage of innovative multi-stage stamping procedures to the assimilation of innovative automation modern technologies, the landscape of metal marking is undergoing a profound makeover. In this dynamic sector, the convergence of advancement and precision is reshaping the possibilities of what can be attained in metal manufacture.
Advanced Multi-Stage Stamping Procedures
Discussing the complexities of innovative multi-stage stamping procedures discloses the sophisticated strategies employed in contemporary production practices. Metal Stamping. Multi-stage stamping is an intricate process that entails multiple actions to change a level sheet of steel right into a final stamped product. Making use of progressive passes away, where different operations are performed at each stage of the stamping process, allows for high precision and efficiency in the manufacturing of intricate steel components
Throughout the first phases of multi-stage marking, the flat metal sheet is fed into the stamping press, where a collection of passes away are made use of to cut and shape the material. Subsequent stages involve additional forming, flexing, and punching procedures to additional improve the component. Each stage is very carefully designed to build upon the previous one, causing the creation of complicated geometries with tight tolerances.
Advanced multi-stage marking procedures require a high level of know-how and accuracy to make sure the high quality and uniformity of the stamped parts. By using advanced equipment and tooling, suppliers can generate a vast array of steel elements with efficiency and precision.
Precision Tooling Innovations
Precision tooling advancements have transformed the metal stamping market, boosting efficiency and high quality in making processes. CNC systems enable for detailed designs to be equated straight right into tooling, guaranteeing precision and repeatability in the marking procedure.
Furthermore, the integration of sensors and real-time tracking abilities in precision tooling has enabled makers to find and resolve concerns promptly, minimizing downtime and reducing scrap rates. By incorporating smart technology right into tooling, operators can optimize parameters such as stress, rate, and placement during the stamping procedure, causing boosted product top quality and raised performance.
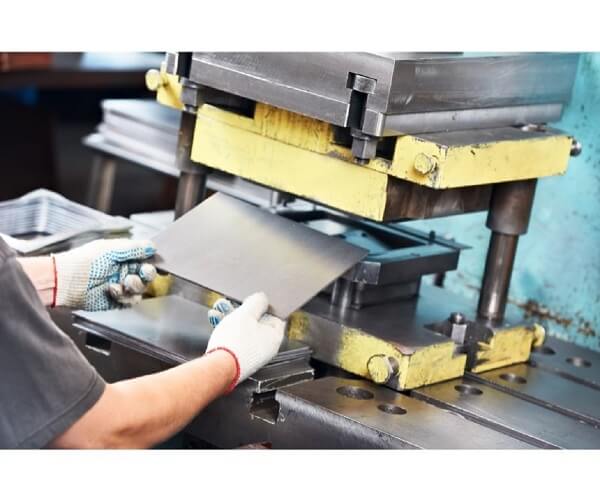
Automation in Steel Stamping
The advancement of accuracy tooling technologies in the steel stamping industry has actually led the method for significant advancements in automation, transforming the production landscape in the direction of enhanced efficiency and productivity. Metal Stamping. Automation in steel marking involves using innovative equipment and robotics to carry out various jobs generally performed by human operators. This change towards automation offers countless advantages, including improved precision, quicker production cycles, and minimized labor expenses
One key facet of automation in metal stamping is the execution of computer system numerical control (CNC) systems, which enable precise control over the marking procedure. CNC innovation enables the development of complex and detailed metal parts with regular site here top quality. In addition, automated systems can be set to run continuously, resulting in greater output prices and shorter preparations.
Furthermore, automation boosts workplace safety and security by decreasing hand-operated handling of heavy materials and decreasing the risk of crashes (Metal Stamping). As manufacturing markets proceed to embrace automation, the future of steel marking holds excellent guarantee for also greater effectiveness and innovation
High-Speed Stamping Methods
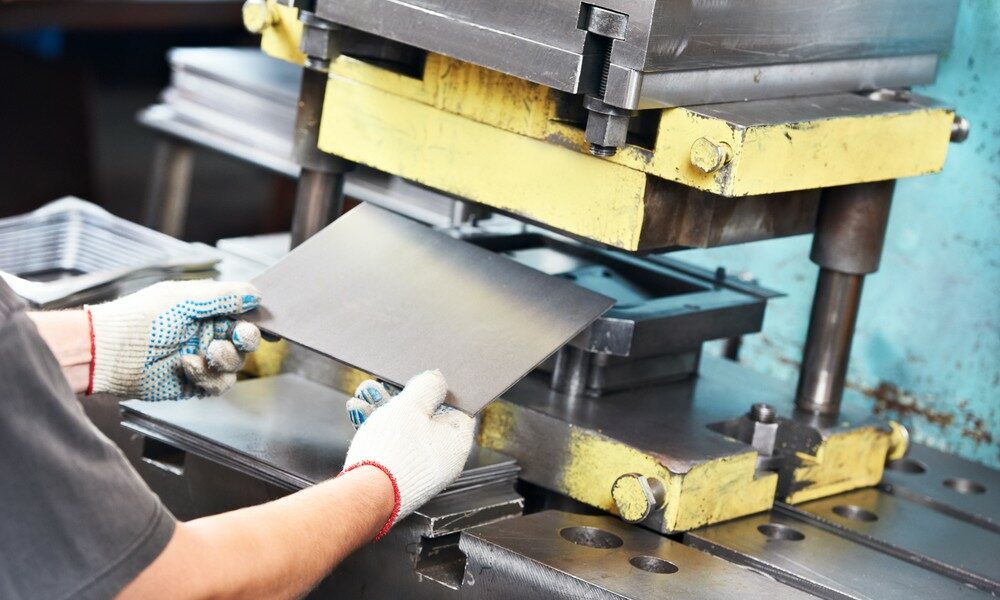
One of the main benefits of high-speed marking strategies is the capacity to generate a huge quantity of components in a much shorter quantity of time contrasted to conventional marking approaches. This raised productivity not just permits suppliers to fulfill limited production web link target dates yet likewise allows expense savings through economic situations of scale. In addition, high-speed marking can assist minimize material waste by enhancing the material usage during the marking procedure.
Moreover, high-speed stamping techniques typically integrate hop over to here innovative features such as fast die change systems and real-time monitoring capacities, better boosting the general efficiency and flexibility of the steel stamping process. As modern technology remains to advancement, high-speed stamping is anticipated to play a critical function in driving the future of precision production.
Quality Assurance in Stamping Operations
Reliable high quality control steps are vital for making sure the reliability and uniformity of metal marking operations. Quality control in marking operations entails a series of organized processes intended at finding and avoiding defects in the produced components. One vital aspect of quality assurance in metal marking is using innovative evaluation strategies such as optical assessment systems and coordinate measuring makers (CMMs) to verify the measurements and tolerances of stamped components.
Additionally, top quality control procedures in stamping procedures frequently consist of the execution of statistical process control (SPC) approaches to check the manufacturing procedure in real-time and guarantee that it stays within acceptable limitations. By assessing data and determining trends, makers can proactively resolve any inconsistencies from the desired high quality requirements.
In addition, quality assurance in metal marking procedures likewise includes thorough material screening to make certain that the raw products utilized satisfy the called for specifications for the stamping process. This may include carrying out product firmness examinations, tensile toughness examinations, and dimensional assessments to assure the quality and stability of the stamped elements. Generally, applying durable quality control steps is vital for attaining top quality stamped parts constantly.
Verdict
In conclusion, progressed strategies in steel marking play an important function in precision manufacturing processes. Via multi-stage marking procedures, ingenious tooling services, automation, high-speed techniques, and rigorous quality assurance actions, suppliers can attain greater levels of precision and performance in their operations. These developments in metal marking innovation have enabled firms to create complex components with limited tolerances, ultimately bring about enhanced product top quality and client fulfillment in the manufacturing industry.